The brazing process plays a critical role in joining metals such as aluminum and copper. The widespread use of these metals in industrial applications requires the application of rigorous quality control techniques to ensure the quality of brazing joints.
1. Visual Inspection
Visual inspection is the first step to detect surface defects in aluminum and copper brazing joints. Visual inspection is carried out using a microscope or magnifying glass and the following errors are detected:
cracks
pores
fluidity defects
heat damage
2. Non-Destructive Testing Methods (NDT)
Non-destructive testing methods are used to detect defects that may occur in the internal structure of the connection.
X-Ray Inspection : It is used to examine the internal structure of aluminum and copper brazing connections. Internal defects, pores and connection errors can be detected by X-ray.
Ultrasonic Test (UT) : Detects errors in brazing connections using high frequency sound waves. It is especially effective in the inspection of thick metal parts.
3. Leak Tests
Leak tests are critical to evaluate the sealing performance of brazing connections.
Air Leakage Test : Air leakage tests, generally performed using Ateq devices, measure the sealing properties of the connections with high precision. These tests are especially important in systems operating under pressure. It is done at low pressures.
Helium Leak Test : This test, performed using helium gas, is one of the most sensitive leak tests. Due to its molecular structure, helium can detect even the smallest leaks. Helium tests are usually done under vacuum and provide the most precise measurements.
Chamber Technology
How does it work? Chamber method is a system in which helium gas is applied into or around the part to be tested and the leaking gas is detected with detectors.
Features and Areas of Use:
Pressurized Chamber : The outer part of the part is pressurized with helium gas. Leaks occurring inside are detected by sniffer detectors located outside.
Areas of Use : Used in testing large and complex structures. For example, aircraft engines, large capacity storage tanks.
Vacuum Chamber : The inside or surroundings of the part are vacuumed and then helium gas is applied. Leaking parts of helium gas are detected with specially designed sniffer detectors in a vacuum environment.
Areas of Use : Ideal for applications requiring high precision. For example, medical devices, semiconductor manufacturing.
Sniffer (Detector) Technology
How does it work? Sniffer detectors are sensitive detectors that detect helium gas leaking around or within the part under test. Helium gas is directed to the detector through a special probe or tube and leak points are detected.
Features and Areas of Use:
Movable Sniffer : A portable device containing a probe that is moved around or focused on the part by the user.
Areas of Use : Ideal for testing small parts or cramped areas. For example, electronic circuit boards, small medical devices.
Fixed Sniffer : These are detectors that work automatically and are fixed around the part under test.
Areas of Use : It is used in mass production on production lines and in situations requiring continuous testing. For example, automotive manufacturing, industrial equipment.
Differences and Advantages:
Chamber Technology : Generally used in testing large parts, the testing process can be more controlled and repeatable.
Sniffer (Detector) Technology : Provides more flexible use and is ideal for testing small and sensitive parts.
4. Mechanical Tests
Mechanical tests evaluate the strength and durability of brazing joints.
Tensile Test : Measures the tensile strength of aluminum and copper brazing connections. Its durability is determined by pulling the connection to its breaking point.
Shear Test : Measures the shear strength of the brazing connection. This test evaluates the joint's resistance to shear forces.
5. Metallographic Examination
Metallographic examination is used to examine the microstructure of brazing joints.
Sectioning and Examination : A section of the connection is taken and examined under a microscope. This inspection detects the homogeneity of the joint, fill rates, pore structures and metallurgical defects.
6. Chemical Analysis
Chemical analysis determines the chemical composition of filler metals and fluxes used in brazing joints.
Spectroscopy : Used to analyze the chemical composition of materials used in aluminum and copper brazing processes. This method checks for correct material usage and compatibility.
7. Thermal Cycling Tests
Thermal cycling tests are used to measure the thermal durability of brazing joints.
Thermal Shock Test : Thermal durability of the connections is evaluated by exposing them to rapid temperature changes. This test is especially important for systems subject to heating and cooling cycles.
8. Explosion Test
Blasting testing is an important quality control method used to measure the durability and tightness of brazing connections.
Burst Test: This test is of great importance, especially in the applications of metals such as aluminum and copper in high pressure systems. Generally, a strength of 3 times the usage pressure is expected. The test piece is discarded.
Conclusion
Quality control techniques in aluminum and copper brazing operations are critical to ensure the reliability and durability of connections. The quality of brazing connections is evaluated in detail using various techniques such as visual inspection, non-destructive testing methods, leakage tests, mechanical tests, metallographic examination, chemical analysis and thermal cycling tests. Correct application of these techniques enables high-performance and reliable brazing connections in industrial applications.
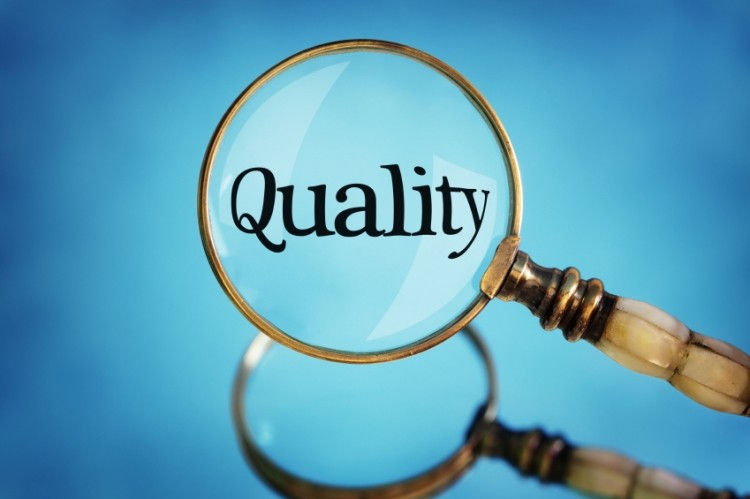
Comments