Introduction
Aluminum brazing is a critical process in manufacturing components for various industries, including automotive, aerospace, and HVAC. This process involves joining aluminum parts using a filler metal with a melting point below that of the base metals but above 450°C. The use of flux in aluminum brazing is of paramount importance. This article examines flux applications in aluminum brazing, its significance, the advantages and disadvantages of varying flux quantities, flux composition, and the alternative of self-fluxing wires in detail.
The Importance of Flux in Aluminum Brazing
Flux is a chemical agent used to facilitate the aluminum brazing process by cleaning metal surfaces, dissolving oxides, and protecting the metal from re-oxidation during heating. The primary functions of flux in aluminum brazing include:
Oxide Removal: Aluminum forms a persistent oxide layer (Al2O3) on its surface when exposed to air, which inhibits wetting by the molten filler metal. Flux helps dissolve and remove this oxide layer.
Surface Protection: During brazing, flux provides a protective barrier to prevent the re-formation of oxides.
Improving Wettability: By cleaning the metal surface, flux enhances the flow and spread of the filler metal, ensuring a strong bond.
Lowering Brazing Temperatures: Flux can reduce the melting temperature of the filler metal during the brazing process, saving energy and making the process more efficient.
Advantages and Disadvantages of Flux Usage Quantities
The amount of flux used significantly impacts the success of the brazing process. Appropriate flux usage ensures strong and durable joints. However, using too little or too much flux has its own advantages and disadvantages.
Using Too Little Flux
Advantages:
Ease of Cleaning: Less flux makes post-brazing residue removal easier.
Reduced Residue: Less flux usage results in fewer residues, potentially improving the final product quality.
Disadvantages:
Insufficient Oxide Removal: Too little flux may fail to adequately remove oxides, leading to weak joints.
Poor Wettability: Insufficient flux can prevent the proper flow and spread of the filler metal, resulting in lower joint quality.
Using Too Much Flux
Advantages:
Effective Oxide Removal: Adequate flux usage ensures complete oxide removal from the surface.
Good Wettability: Sufficient flux improves the flow and spread of the filler metal, creating strong and durable joints.
Disadvantages:
Difficulty in Cleaning: Excess flux can make post-brazing residue removal challenging.
Increased Costs: Using too much flux can raise the process costs.
Corrosion Risk: If flux residues are not adequately cleaned, they can cause corrosion.
Flux Composition
Aluminum brazing fluxes typically consist of alkali fluorides, chlorides, and other compounds. A typical aluminum brazing flux composition may include:
Potassium Fluoride (KF): Assists in dissolving the oxide layer.
Lithium Fluoride (LiF): Enhances the effectiveness of the flux due to its low melting point.
Potassium Chloride (KCl): Improves fluidity, aiding in the spread of the filler metal.
Sodium Fluoride (NaF) and Sodium Chloroaluminate (NaAlCl4): Support oxide dissolution and surface cleaning.
Self-Fluxing Wire Alternatives
Self-fluxing wire is a type of filler metal that contains flux within the wire. These wires simplify the process by eliminating the need for manual flux application and offer several advantages:
Convenience and Efficiency: The presence of flux within the wire speeds up the brazing process and makes it more efficient.
Controlled Dosage: Pre-measured flux ensures neither too much nor too little flux is used.
Cleaner Process: Self-fluxing wires minimize flux residues, reducing the need for cleaning.
However, there are also disadvantages to self-fluxing wires:
Cost: These wires can be more expensive than standard filler metals.
Application Limitations: They may not be suitable for all brazing applications and might underperform in specific scenarios.
Conclusion
The use of flux in aluminum brazing plays a crucial role in forming successful and durable joints. Flux provides essential functions such as oxide removal, surface protection, and improved filler metal flow. However, the quantity of flux used must be carefully controlled, as both insufficient and excessive flux can negatively impact the process quality. Additionally, the composition of flux and alternatives like self-fluxing wires should be considered in the brazing process. All these factors directly affect the final product quality and process efficiency.
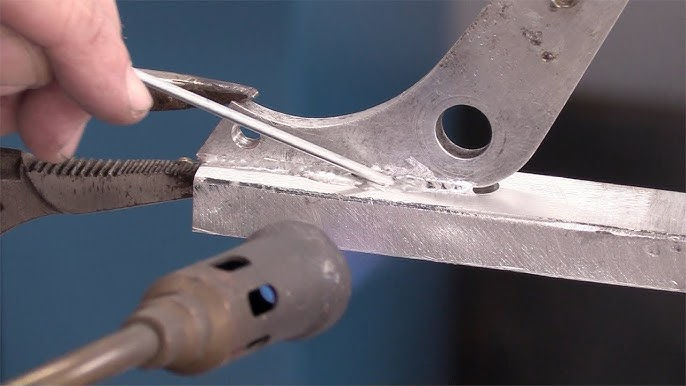
Hangisini Tercih Edersiniz?
Düşük Maliyet Varyasyonlu Kalite (Operatör İnsiyatifi)
Orta Maliyet Daha az Varyasyonlu Kalite (Dozajlama Makinesi)
Yüksek Maliyet Yüksek Kalite (Kendinden Fluxlı Tel)
Comments